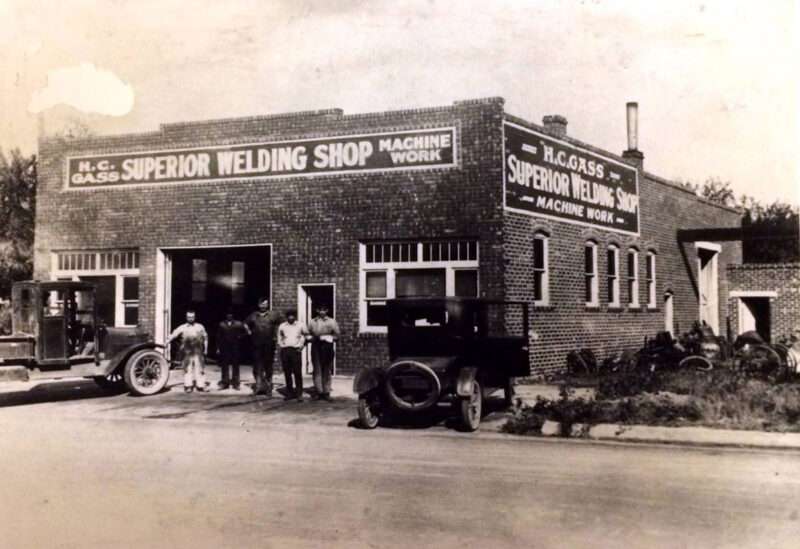
Welcome to Hutch Post’s new feature series "A Day in the Life." We've gone behind the scenes to see what "a day in the life" is like for some of Reno County's busiest shops, factories and businesses. We'll show the inner workings of facilities you may pass every day, to finally see what goes on inside. From boilers to donuts, join us as we learn how things are designed and produced right here in Reno County with "A Day in the Life." This series will be posted every other Sunday morning.
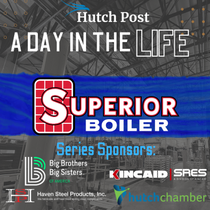
By ROD ZOOK
Hutch Post
HUTCHINSON, Kan. — Superior Boiler has been a part of Hutchinson for more than 100 years. The company started as a welding shop and quickly grew to the company it is today. The company just completed a major expansion last year with the relocation of its watertube boiler facility from Richmond, Virginia, to Hutchinson.
The company manufactures industrial watertube and flextube boilers, scotch marine and vertical firetube boilers for process steam, hot water and waste heat recovery, and high-efficiency hot water condensing boilers. In addition to boilers, Superior Boiler also manufactures boiler room equipment items and parts, and provides 24-hour service. Superior Boiler employs approximately 150 people at its Hutchinson locations.
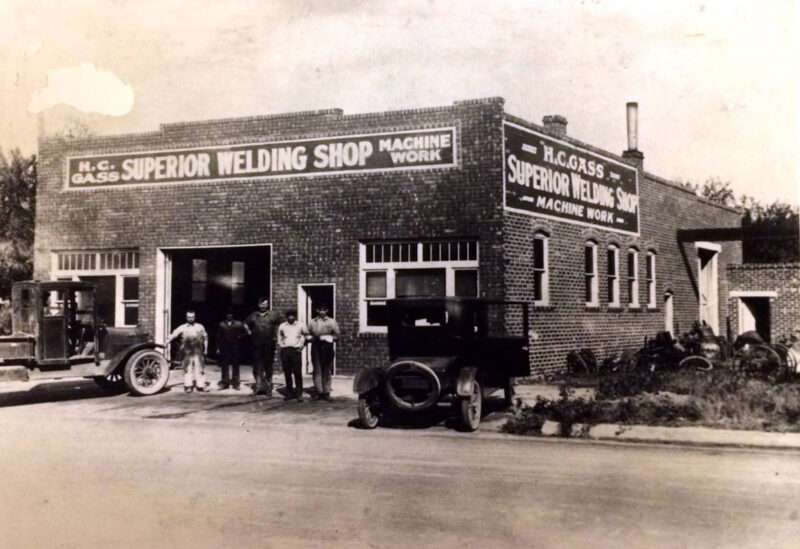
The company is in a unique situation compared to most manufacturers. That’s because Superior Boiler still relies heavily on non-computer controlled welding. Many of the components on the products the company makes are hand welded. The need for such skilled labor is great.
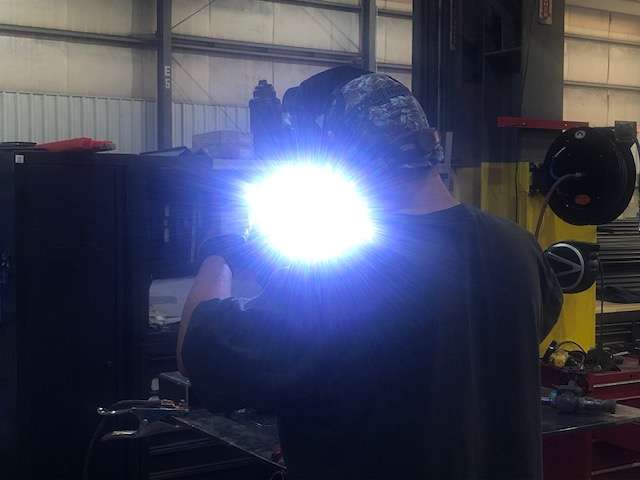
The making of boilers is a long and complex task, whether it's a firetube boiler or a watertube system. For a firetube boiler, it starts with taking a solid sheet of steel and fabricating it into a large vessel. In the watertube area, it means fabricating tubes that will be carried inside a very large containment area. Both require dozens of steps.
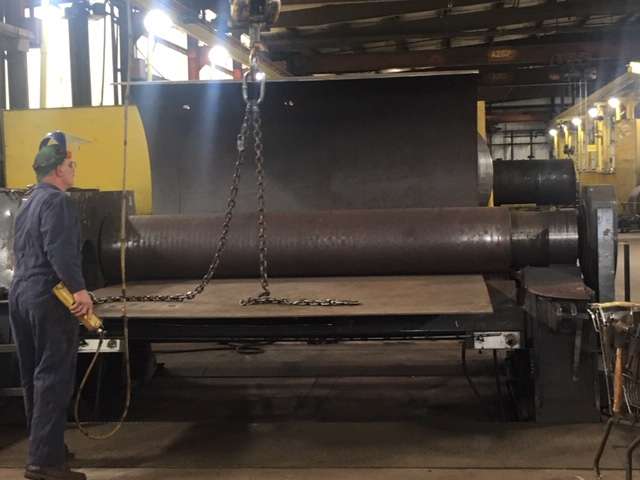
Each boiler starts in a design room where space needs are determined. How the boiler is going to service the facility is also determined. The process is necessary because each boiler is handmade to fit into a particular space. Each boiler has its own book of instructions, blueprints and details of how it will be built. Each step is closely watched by a quality control person.
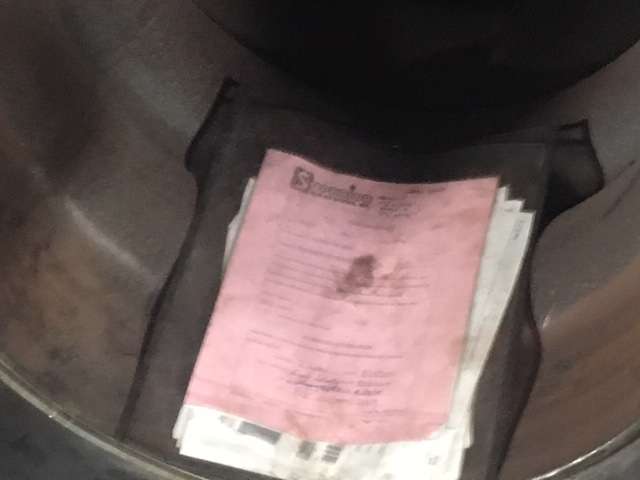
Once each step is finished, it is signed off and even stamped onto the boiler. The book moves from step to step with the boiler throughout its manufacturing process.
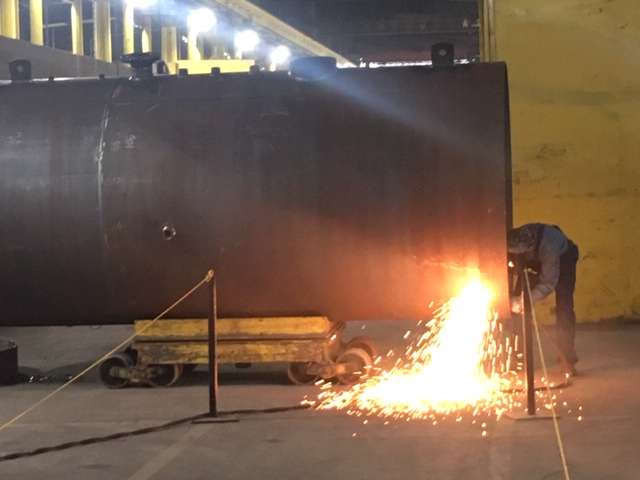
Because no two boilers are alike, manual welding is so important to the company. While most of the boilers are made by hand, there are computers that cut parts and pieces as needed.
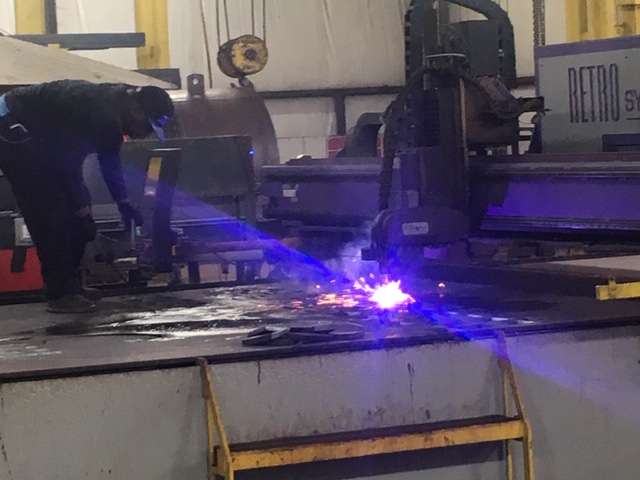
Another machine in the watertube division can be programmed to bend steel tubes into a specific configuration to fit into a particular design.
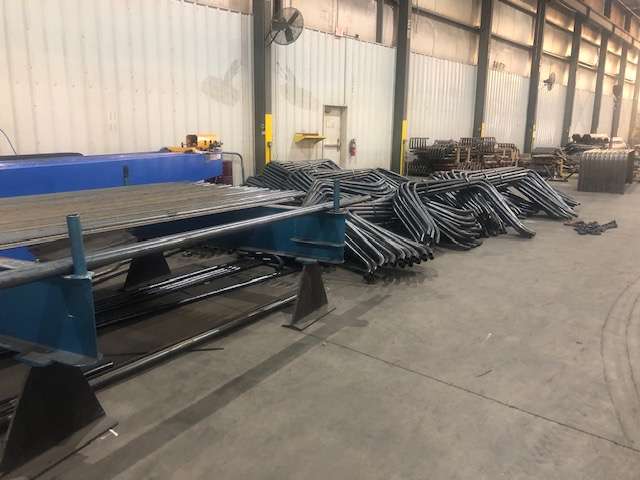
The process for a firetube boiler versus a watertube system is very different. The watertube systems are extremely large and are built inside a housing. Some designs use a flatbed trailer. That trailer becomes a permanent part of the system once it is delivered to its location. A conventional boiler is also large, but is shipped by truck and then placed in its designated location.
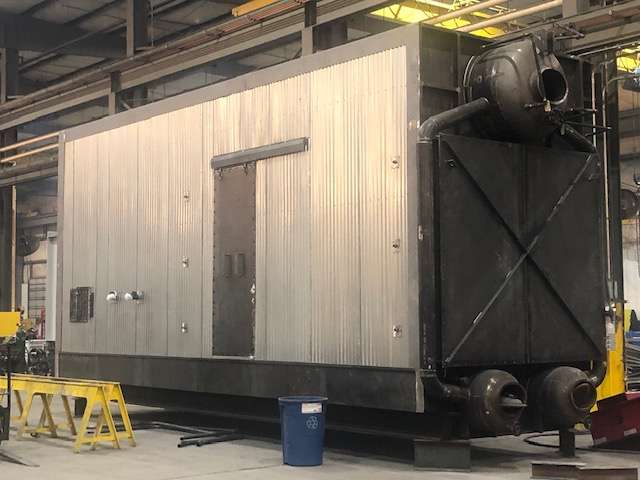
Once the tubes are in place, the vessel is fitted inside the holding area and the rest of the system is assembled. This requires some very heavy lifting of steel plates that weigh several thousand pounds. Gantry cranes move back and forth across the facility doing the heavy lifting.
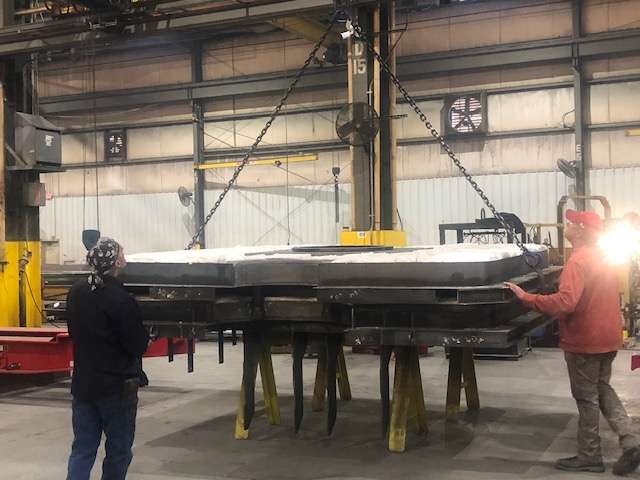
On a firetube boiler, the vessel is welded on until all connections are attached. The vessel then moves into an oven where it is heated to 1,100 degrees. That hardens the welded connections, making the boiler stronger.
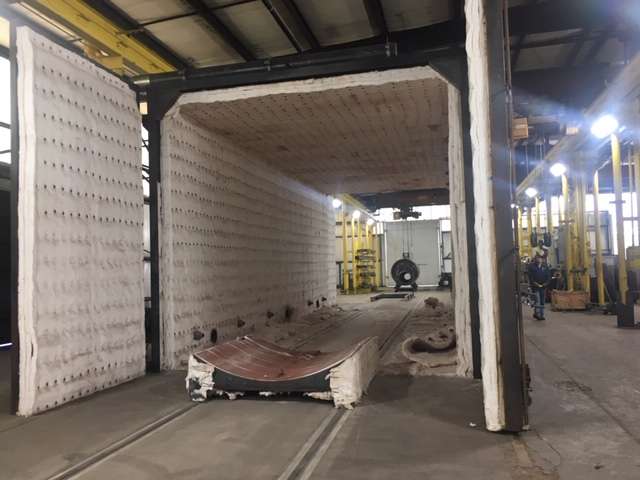
Once that process is finished, the vessel moves across the street for its final assembly and painting. The boiler’s controls and valves are installed and the boiler is painted either in traditional Superior Blue or whatever the customer orders. All of the components in this area come from vendors.
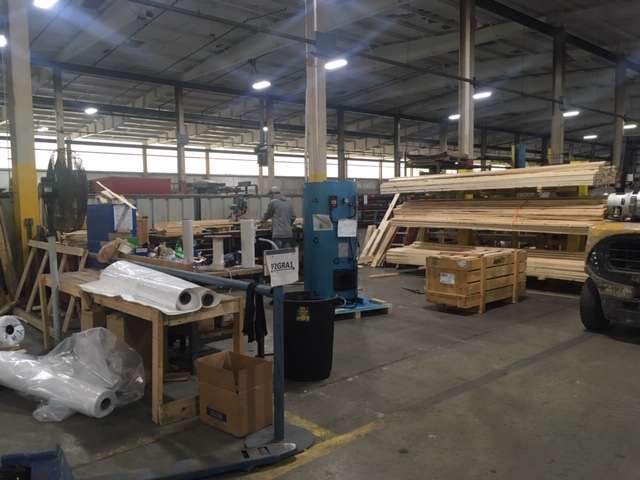
The area has its own shop where any part can be made, including one-of-a-kind parts as needed. The area even has its own wood shop to build the shipping crates needed to transport orders. The shop has carts to transport parts and pieces that will be assembled in the main plant. Each has a number matching the vessel across the street.
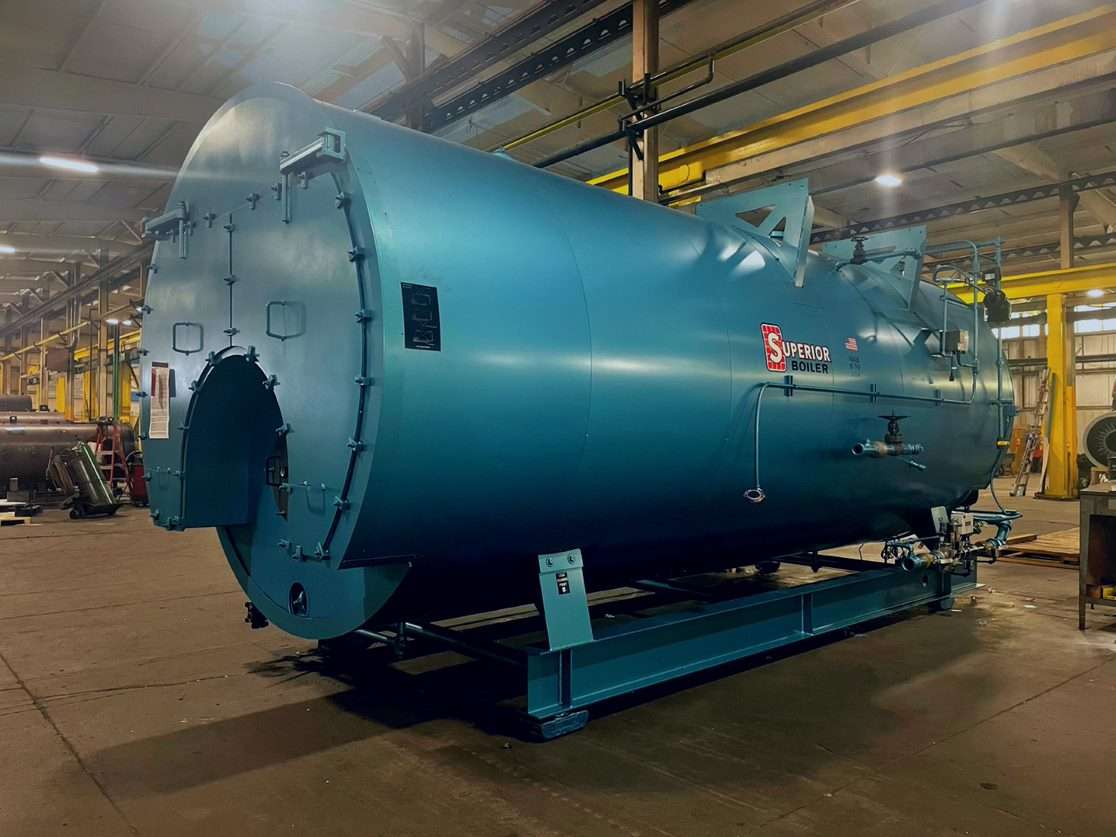
Each boiler can take 14-20 weeks to complete, depending on its size, and can weigh up to 60 tons. Watertube boilers can take up to 32 weeks to complete. They are shipped all over the world. Superior has a strong order list, but is fighting to find the skilled labor it needs to fulfill those orders — a problem many in the industrial sector are facing.
If your business or industry would like the opportunity to show off how you do things, contact Rod Zook at [email protected] or call 620-259-7396 and be a part of "A Day in the Life."
A Day in the Life is brought to you by:
Hutchinson/Reno County Chamber of Commerce
Kincaid Manufacturing
JW Machine
Haven Steel
CLICK HERE TO SEE THE FULL SERIES
CLICK HERE to download the Hutch Post mobile app.
CLICK HERE to sign up for the daily Hutch Post email news update