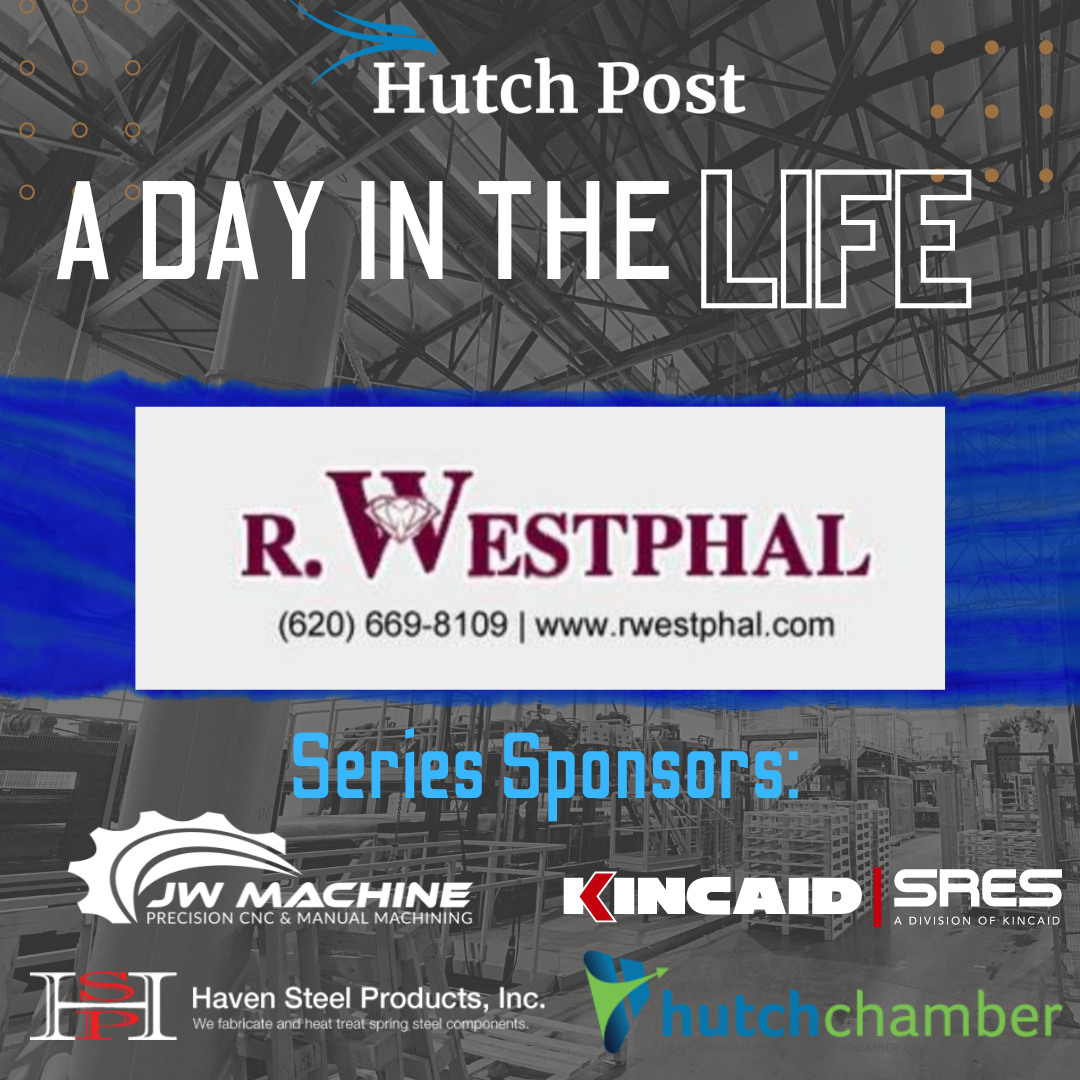
Welcome to Hutch Post’s new feature series "A Day in the Life." We've gone behind the scenes to see what "a day in the life" is like for some of Reno County's busiest shops, factories and businesses. We'll show the inner workings of facilities you may pass every day, to finally see what goes on inside. From boilers to donuts, join us as we learn how things are designed and produced right here in Reno County with "A Day in the Life." This series will be posted every other Sunday morning.
By ROD ZOOK
Hutch Post
HUTCHINSON, Kan. — “I have a passion for jewelry, not so much to wear it, but the artwork of it. The dense work fascinates me. The passion is for making it, repairing it, handling it, and mostly seeing the joy that comes from people’s faces when I hand them a piece of jewelry I made or repaired, and they say, ‘Wow, what a beautiful job.'” —Richard Westphal.
The name Westphal has been synonymous with the jewelry business in the area for many years. And while Richard Westphal of Westphal Jewelers in Hutchinson is there to do business, it is his love for designing pieces and repairing precious items that he loves most.
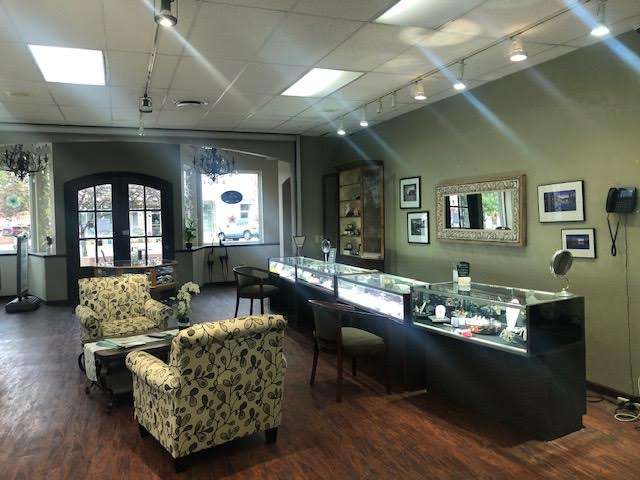
He is part of a third generation family business providing Gold & Diamond Jewelry, Gemstone, Sterling Silver Jewelry, Engagement Rings & Wedding Bands, Bridal Sets, Westphal Jewelry, Platinum Bands, 14Kt White Gold Jewelry, and Custom Jewelry Design. It’s that custom jewelry design that gets Westphal and his daughter, Katie, inspired each day. From a small workshop in the back of the store in downtown Hutchinson, both design, repair and build pieces of art that they sell and use in competitions too. The duo sees the art of jewelry design quite differently as the elder Westphal is more traditional in design while Katie tries to think outside the box a little more.
The process starts with a design. Most of the designs are simply drawings on paper where they take ideas from a customer or come up with their own depending on what that customer wants. From there, the process of building the piece begins. The design is made from wax. That wax piece is cast in plaster inside a small mold. The mold is then heated in a casting oven to 1,000 degrees for five hours. In that process, the wax melts, but leaves the impression in the casting.
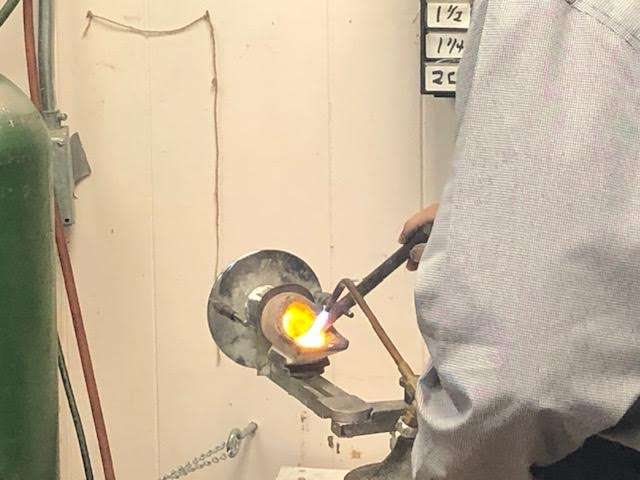
While there are more advanced ways to fill the mold with molten gold or silver, Westphal uses a very old manual centrifuge. Gold is heated in a small, open crucible until it is molten. The small casting is placed in a holding and, when ready, the centrifuge is released from a loaded position and spins, forcing the gold into the casting. Once that is done, the mold is quickly cooled and the casting material is removed, leaving the rough product.
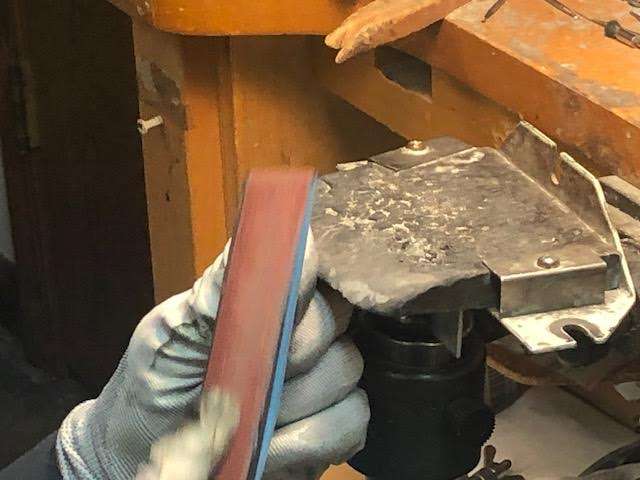
The material is ready to be finished using a file and buffing wheels until the piece is ready to have any type of stone or decoration attached. That too is done either by a very steady hand or by a laser-soldering system that can attach prongs of other metal pieces to the main work. Both are used by the Westphals.
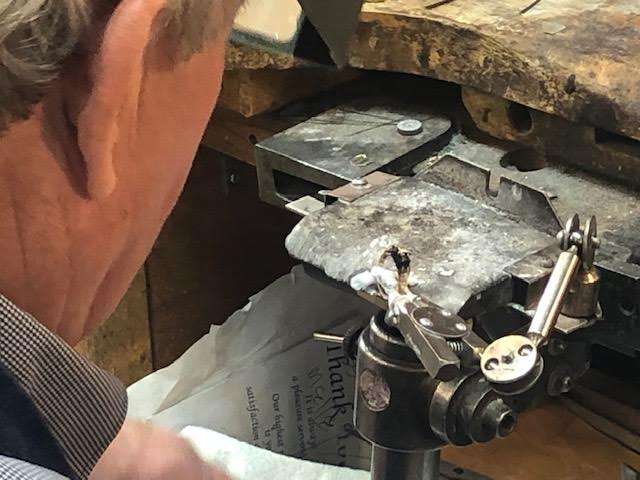
Once the piece is ready, the stone or stones of choice are attached and the piece goes through a final touchup before it is ready to be delivered or put up for sale. The Westphals go from show to show both showing their work and looking for various stones or other things that can be made into jewelry.
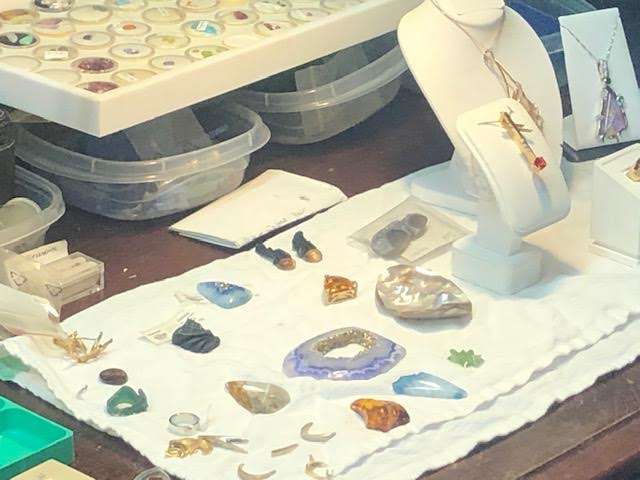
While there is an education process you can go through to learn the art of jewelry making, Westphal says one of the best ways is simply through an apprenticeship. It's a love his family has been passing down from generation to generation.
A Day in the Life is brought to you by:
Hutchinson/Reno County Chamber of Commerce
Kincaid Manufacturing
JW Machine
Haven Steel
CLICK HERE to download the Hutch Post mobile app.
CLICK HERE to sign up for the daily Hutch Post email news update.