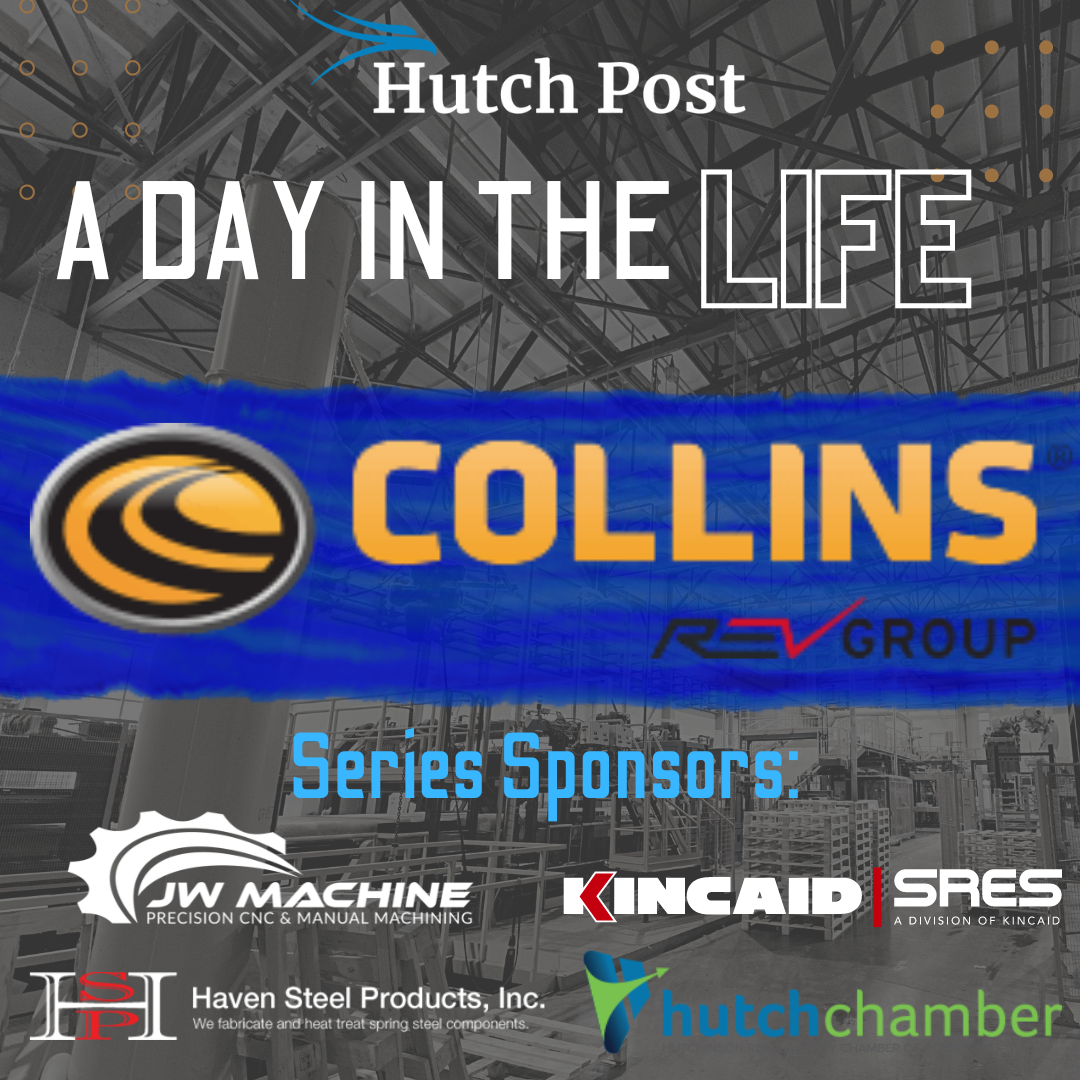
Welcome to Hutch Post’s feature series "A Day in the Life." We've gone behind the scenes to see what "a day in the life" is like for some of Reno County's busiest shops, factories and businesses. We'll show the inner workings of facilities you may pass every day, to finally see what goes on inside. From boilers to donuts, join us as we learn how things are designed and produced right here in Reno County with "A Day in the Life." This series will be posted every other Sunday morning.
ROD ZOOK
Hutch Post
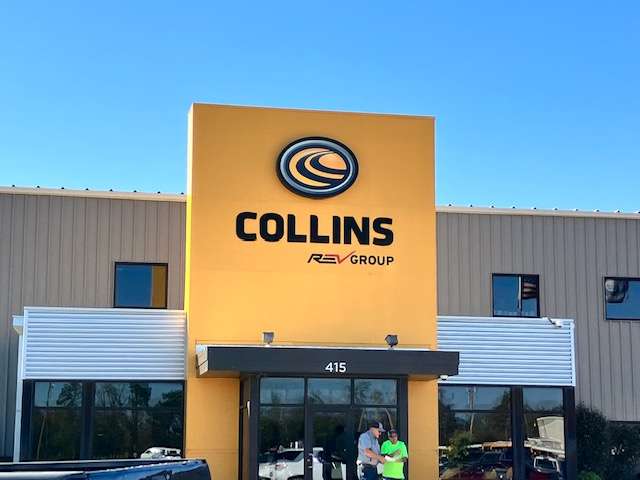
HUTCHINSON, Kan.— After starting as a company to fill a niche in school transportation, Collins Bus has grown and endured as one of the nation's leading small bus manufacturers.
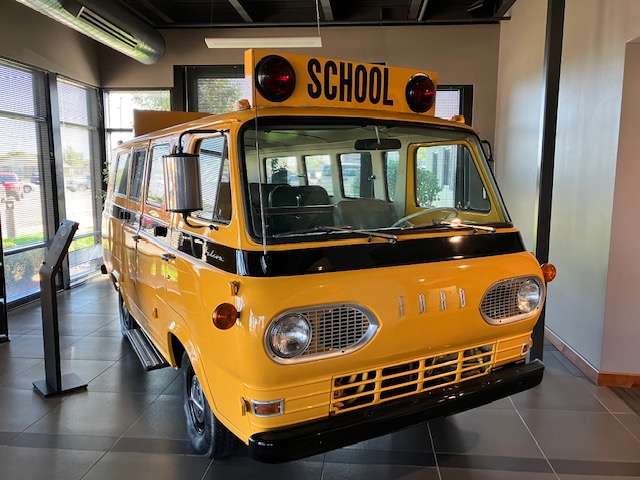
Founded by Don Collins Sr. as E-CON-O Conversion in Kansas, the company built the first Type A School Bus. Five years later the company moved to Hutchinson as Collins Industry. Through the 1980’s Collins quickly became the leader in small special needs transportation.
There are many steps to building a school bus. It all starts with the materials. They are housed in a pre-assembly area. The parts are made to order and shaped, including the steel skin of the bus.
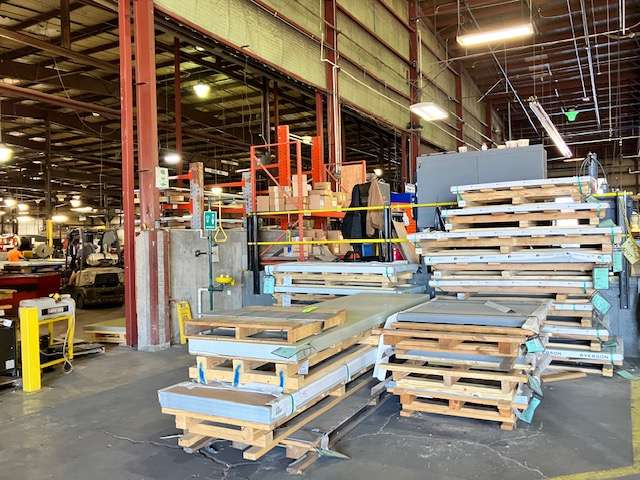
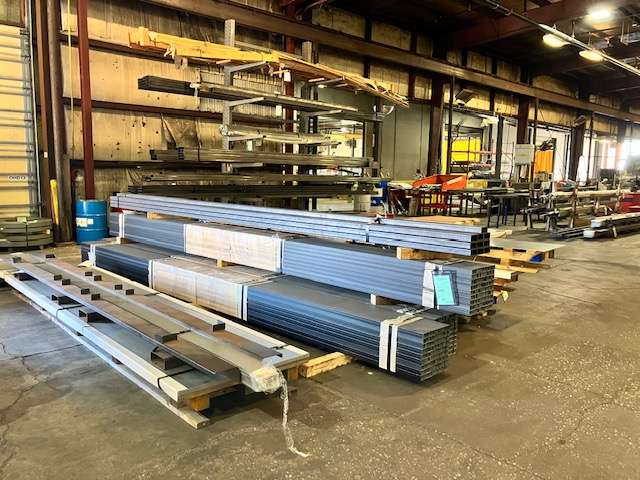
Giant mechanical punches cut through the steel skin and bend it into shape. At the same time the inner assembly is being put together as welders assemble the steel roll cages and roof.
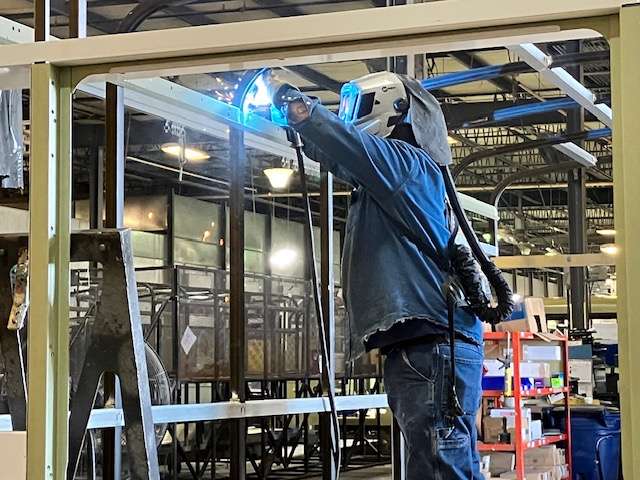
The skin is both riveted and glued into place with a strong adhesive.
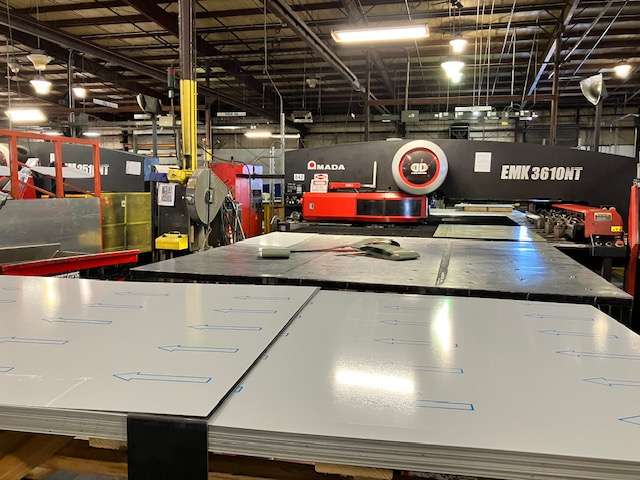
A third area is preparing the chassis for final assembly. The parts all converge on an assembly line where the skin and the cage are brought together.
The assembly is painted to color and all of the internal parts are placed inside the vehicle body including seats, windows and mechanical components and fixtures.
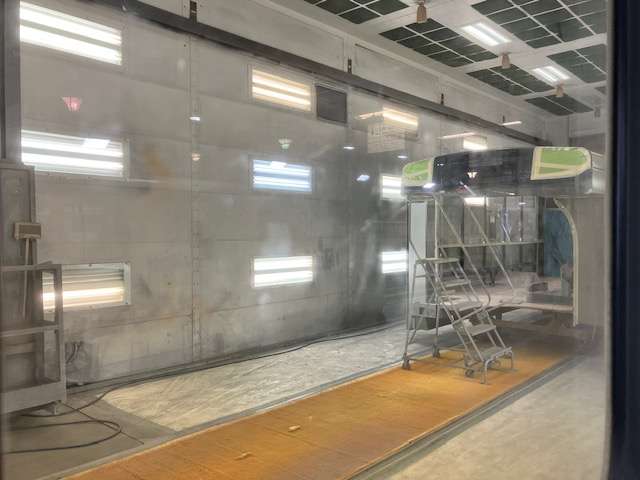
Once all of that is finished, the entire body assembly is lifted onto the chassis.
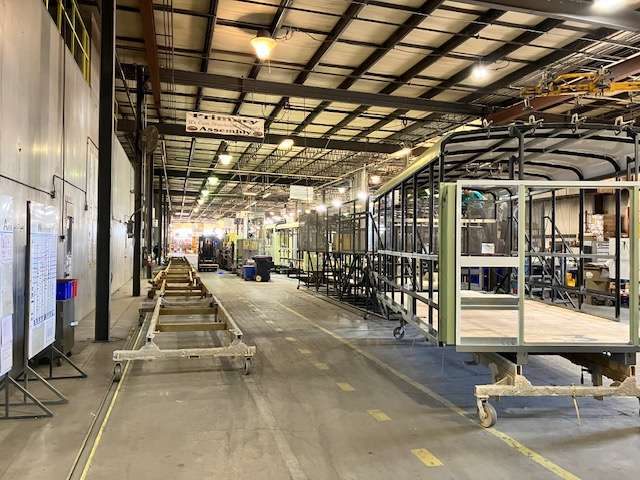
Once that is finished, the product goes through a number of quality control steps and the finishing touches are put on the bus such as decals, an undercoating to protect the chassis and any remaining touches that are unique to that order.
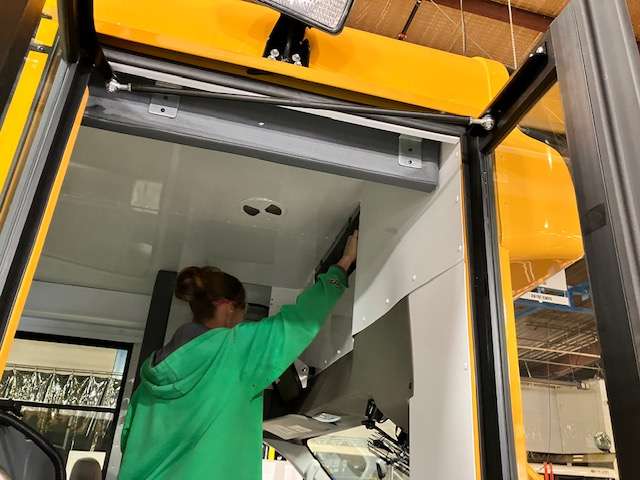
Collins has been able to adapt to the changing needs of its industry, including E-buses, propane powered vehicles and even emergency vehicles for a time.
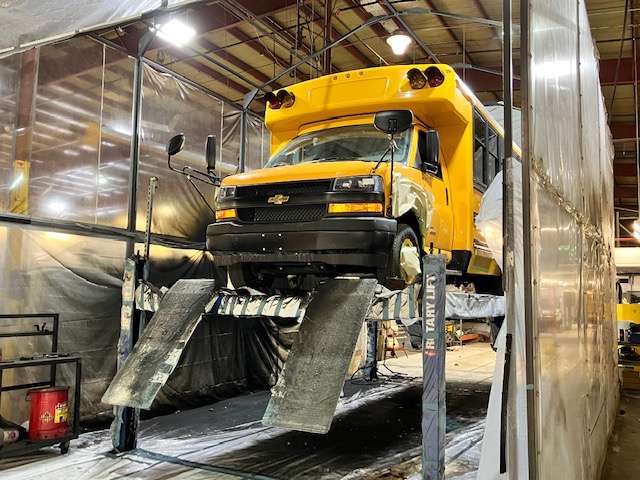
The plant also has continued following a purchase by REV Group in 2006. Collins has become the largest chassis inventory of Type A bus products.
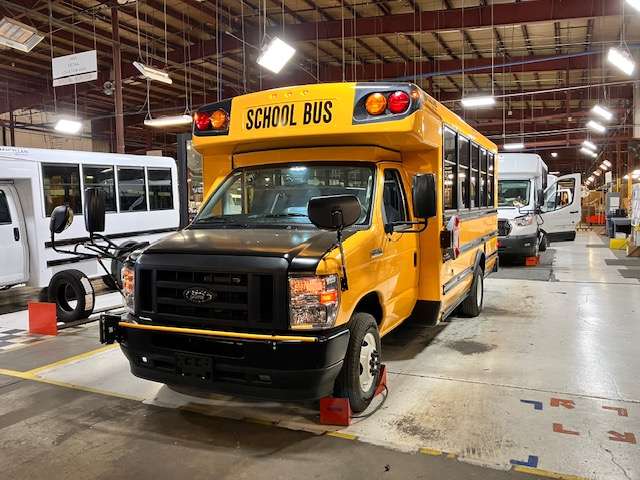
Collins is still looking for assembly and skilled workers and the hope is that they can increase workforce numbers and keep assembly moving forward.